According to an EU study (“Compressed Air Systems in the European Union”), in 80% of all enterprises the compressed air distribution systems are the weakest link in compressed air technology. This means that each year thousands of euros are literally blown out of the window for energy costs.
Compressed air distribution has the job of transporting the energy carrier compressed air with as little impact as possible on the
- Air quality (owing to rust, water, welding scale etc.)
- Flow pressure (owing to uneconomical pressure losses) and
- Quantity (owing to unnecessarily large leaks).
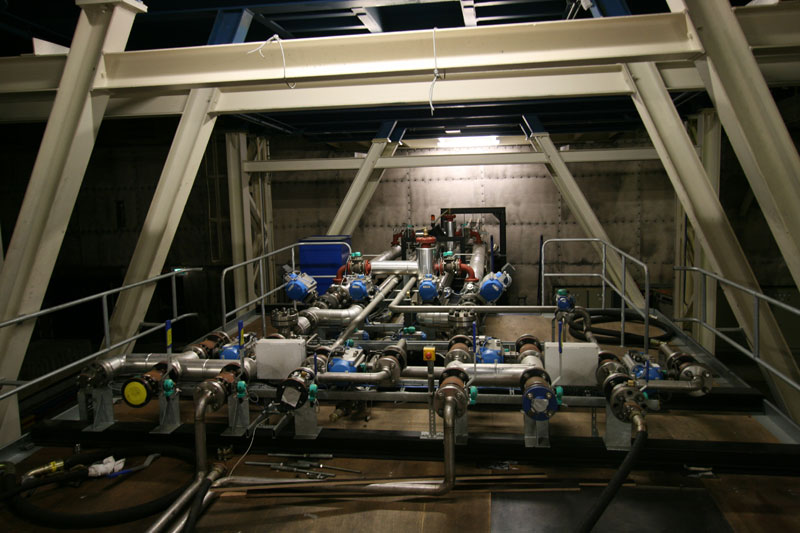
In many facilities, compressor systems often get little attention from engineering and maintenance staff because process equipment, electrical power, HVAC and steam systems normally occupy more of their time. The main technical priorities for a plant compressed air system should be:
- Manufacturing process reliability (air quality)
- Compressed air system cost control
A technical assessment of the piping distribution system and identifying high ‘point-source’ surge demand conditions should be the first order of business if low air pressure in manufacturing is a major issue. Repairing air leaks and installing additional compressors and expensive controls will not rectify a basic pipe distribution system or process machine operational issue. Having too many compressors in service, needing equipment maintenance work, upgrading controls and repairing large leaks certainly are issues that need to be addressed. However, do not allow improperly sized air piping and fittings at one or two process machines in your plant to dictate a higher pressure for the entire system. Be sure that your Compressed Air System Assessment Team flies their ‘helicopter’ far enough above the trees to see all of the forest.
IS YOUR INTEREST AROUSED?
- Do you want to know more?
- Or do you now think that your compressed air network requires a new roof over it?