The Thompson Europac boiler is suitable to fire a range of solid fuels (single fuel firing, as supportive to the main fuel, or a mixture). Some of which are:
Wood chips, wood pucks, wood pellets, coal, coal briquettes, corn cobs, spent grain, rice husk pellets, palm kernel shells, tobacco stem, sunflower husk, peach pips, bamboo chippings, cashew nut shells, macadamia nut shells, torrefied bamboo pellets, torrefied wood chips.
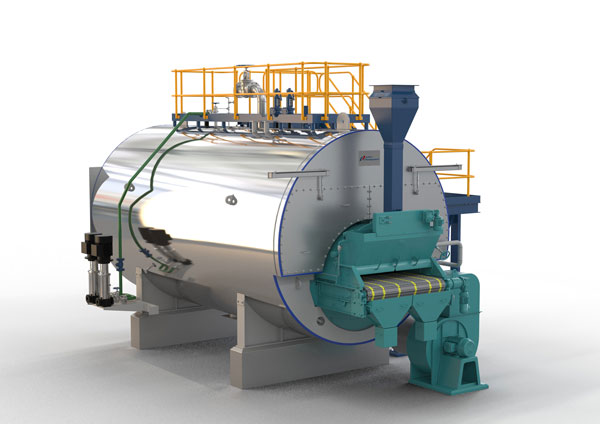
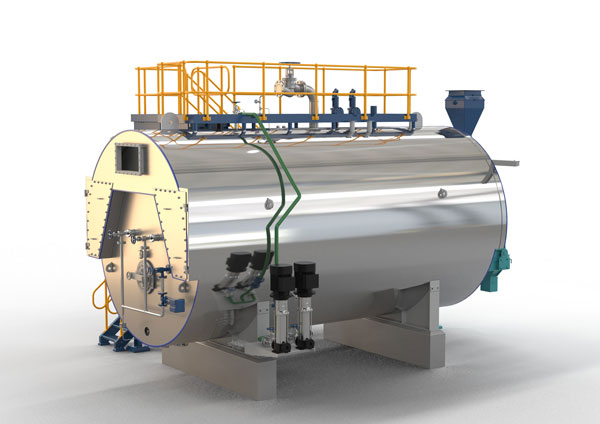
Features:
- Horizontal boiler shell, rolled and welded, with flanged end plates and reversal chamber mounted by stay bars
- Full 3-pass boiler and wet-back furnace design
- Two convection passes with spiral-tube technology, increasing heat transfer and reducing fuel consumption by up to 2.5%
- Corrugated/Bowling hoop furnace design allowing for side secondary air supply, added rigidity and improved.
Heat Transfer:
- Designed and manufactured in accordance with the latest Health and Safety standard EN12953
- EuroBMS integrated boiler management system, controlled through physical operator control elements
- EuroBMS combustion management, optimized automated fuel-air ratio for solid fuels
- Trusted Thompson Triumph chain grate stoker(-s)
- Floor mounted Induced Draught (ID) fan (including manual banking damper) designed for total system pressure
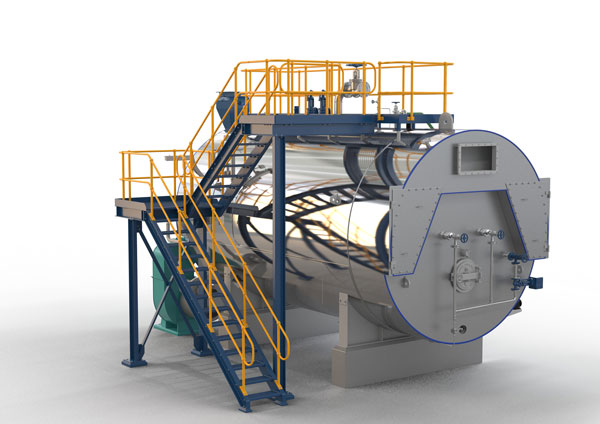
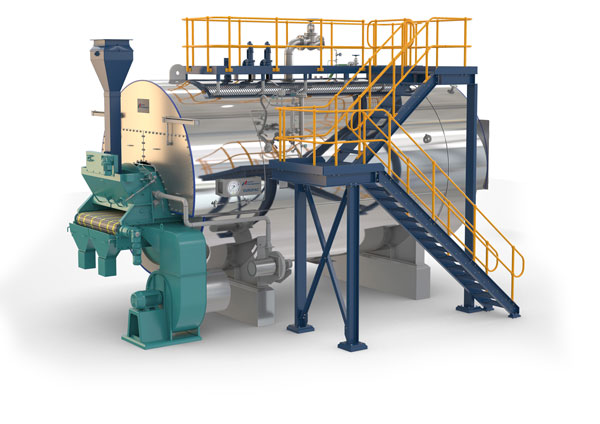
Compensation:
- Manually retractable steam soot blowers to clean the tube plate in the reversal chamber
- High integrity cut-out and lock-out safety systems
- Stainless steel grade 430 Finish 2B cladding
- Standard cable trays and integral pipework
- Lloyd’s inspection and certification
Thompson Triumph chain grate stoker
Features:
- Reliable and durable construction
- In-house casted Meehanite chains links and side seal blocks
- Integrated primary air distribution vanes
- Swinging chute for even fuel feeding and optimal combustion
- Forced draft (FD) fan for primary combustion air supply through the chain grate
- Side secondary air supply system (SSA)
- Front secondary air supply system (FSA)
- Dead plate primary air supply system (DPA)
- Proven EuroBMS combustion management
- Planetary stoker drive gearbox with electronic torque trip protection
- Variable speed driven fans for reduced electricity consumption, fan wear, and noise
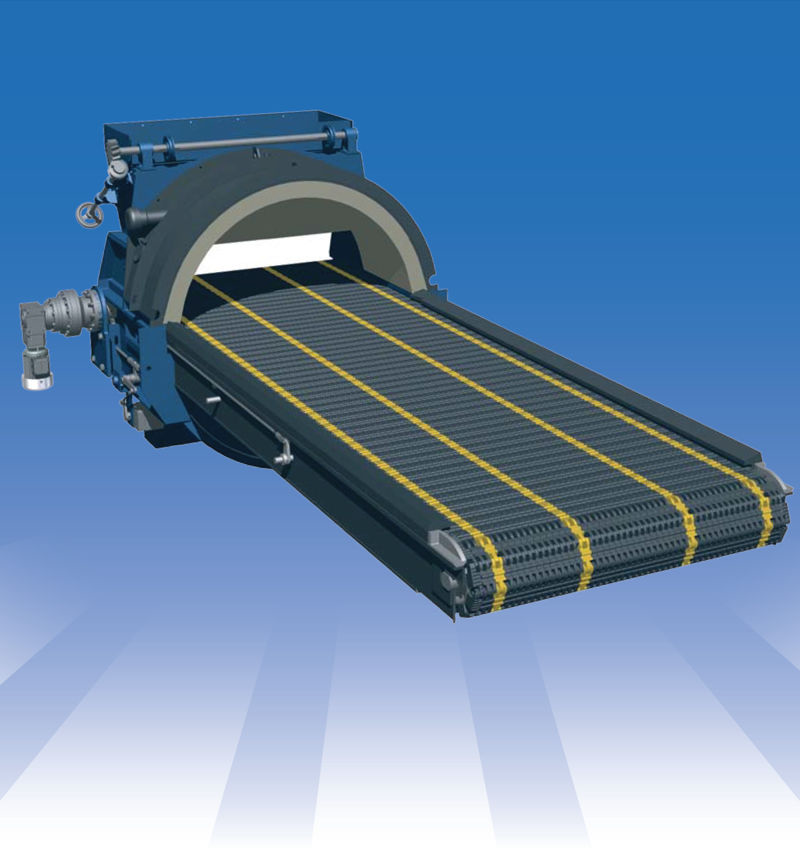
Side secondary air supply system
Secondary air is brought into the combustion zone from the side of the stoker to create turbulence and trap airborne volatiles and particles. It also adds oxygen to target aerial volatiles and burn them before leaving the furnace. This results in a cleaner and more efficient combustion and dramatically reduces exhaust gas particles and emissions. It is especially effective for high volatile fuels and situations where an increased residence time in the combustion zone is required.
Front secondary air supply system
Additional secondary air is introduced from the ignition arch above the incoming fuel to assist in the ignition process. This process makes it easier for the volatiles in low calorific fuel types to be released, prevents runaway fires at low load.
Dead-plate primary air supply system
Fuels with a high moisture content can be dried and prepared for optimal combustion by introducing primary air in the front of the stoker. The air is blown through holes in the dead-plate and enters the fuel right after it is deposited onto the stoker. The release of volatiles and mixing it with the incoming air assist the start of the combustion process in the low oxygen zone under the ignition arch.
Note:
John Thompson recommends a fuel surge hopper to feed into the swinging chute and provide support to hang the swinging chute from.